If wind mitigation and stronger homes are the paths to reducing insurance claims and bringing down insurance premiums in hurricane-prone areas, as a growing number of industry experts believe, then homeowners, builders and insurers may want to take a look at some homes rising in the Florida Panhandle.
They’re not the pricey, igloo-shaped “windproof” homes found in some beach areas, but are designed to be affordable – with gables and a roomy front porch like most conventional homes. The houses have been built with reinforced concrete walls, heavier roof decking, more fasteners per foot, impact-resistant windows and doors anchored directly to the concrete, as well as standing-seam metal roofs designed to withstand hurricane-force winds.
And the construction work is frequently and thoroughly inspected, more than what municipal building departments and state mitigation plans can offer, builders and inspectors say.
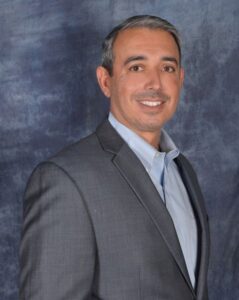
“I won’t say they’re hurricane-proof – but hurricane-resistant,” said Darius Grimes, president of Disaster-Smart, a firm that audits and inspects homes built to the Insurance Institute for Business and Home Safety’s famously stout FORTIFIED building standard.
At one of the homes nearing completion in Pensacola, the exterior walls are thicker than most wood-frame structure walls. The construction is sort of the reverse of the better-known technique called insulated concrete forms, or ICF, which uses polystyrene foam blocks as forms for poured concrete. The new system, made by ConcreWallUSA, now known as Fortified Structural Solutions and based nearby in Panama City, Florida, has a polystyrene core – with steel remesh and sprayed-on concrete on both sides.
The approach is so new that some insurance carriers are still scratching their heads on how to classify it.
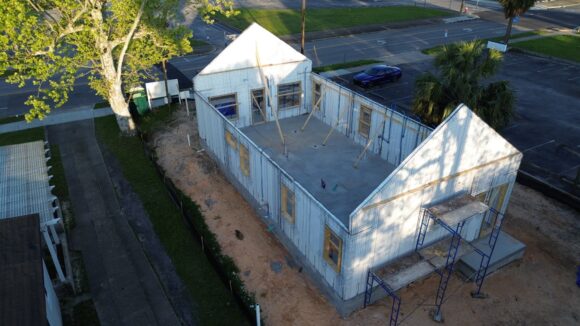
“Every carrier I talked to said to go ahead and write it as a masonry structure, and we may have to figure something out later,” said Suzanne Pollard Spann, CEO of Legacy Insurance Brokers in Pensacola.
Spann has obtained quotes from Olympus Insurance and others. And, despite some unfamiliarity with the new wall system, carriers do appear willing to provide significant premium discounts for the property, she noted. The Spring Street home near downtown Pensacola is about 1,500 square feet and is valued at about $400,000. The average quoted annual premium is about $1,600, Spann said.
Comparable-sized homes in the neighborhood, built with conventional wood framing and shingle roofs, have seen HO premiums as high as $7,000 a year, Spann said.
Besides wind-resistance, the Concre wall system also offers excellent fire resistance, triggering further premium credits on homeowner policies, Grimes pointed out.
The idea of building rock-solid homes at an affordable price in a place that has seen its share of hurricanes is largely the brainchild of the Home Builders Association of West Florida. Spann served on the board in 2023 when the project began.
“This is my pet project because of what it can mean for our industry,” Spann said.
The home’s builder is Amir Fooladi, of ParsCo builders, who was president of the local HBA in 2023. It’s one of the first homes in Florida to be built with the ConcreWall system.
Fooladi, Spann and the HBA worked with city officials and with the non-profit Habitat for Humanity to launch the project and at least two others like it. So far, more than 40 local and national companies have donated funds, labor and/or materials for the site. Once completed and sold to a Habitat family, any profits will go back to the Home Builders Association.
“I feel like this can be a model for all home builders associations,” Fooladi said.
Part of the reason behind building the concrete homes is to get an idea of the costs and the challenges involved in constructing houses to a stronger standard, Grimes said. But Fooladi said it is difficult to gauge the exact cost since so much material has been donated. According to estimates from the National Association of Home Builders, Reddit, and HomeGuide.com, concrete-walled structures can cost up to $250 per square foot to build — about 50% more than conventional homes.
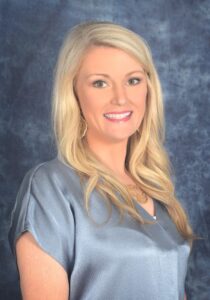
The higher build cost will pay for itself in lower insurance premiums, reduced cooling expenses, and reduced repair costs, advocates say. It’s not just the structural concrete that makes these types of houses so strong, Fooladi and Grimes explained. The building has to meet the IBHS FORTIFIED standards, which often require more wind-resistant material and building techniques than Florida’s own vaunted building codes. While most building codes require roof-decking nails to be placed every 6 inches, the FORTIFIED certification requires nails every 4 inches, Grimes explained.
But the biggest difference is that FORTIFIED-approved homes must be inspected more thoroughly and more often, then reinspected years later, he noted.
“Building codes are only as good as the local inspector,” said Carl Schneider, a Gulf Coast insurance agent who is familiar with the Florida Panhandle and Alabama markets. “FORTIFIED homes are way above the Florida building codes on that.”
He pointed to a recent study by the Alabama Department of Insurance and the University of Alabama’s Center for Risk and Insurance Research that found that FORTIFIED-built homes fared significantly better in Hurriane Sally, which hit southern Alabama and northwest Florida in 2020. Insurance company payouts would have been about 75% less if all impacted homes in two coastal Alabama counties had been built to the standards, the study found.
The FORTIFIED approach is spreading nationwide, and it’s about to become a little tougher for some contractors. Starting Nov. 1, all FORTIFIED-approved homes must be installed by FORTIFIED-certified roofing contractors, according to the IBHS. That means the contractor must complete IBHS training courses and follow a rigorous protocol when installing roofs and roof decking.
Top photo: Darius Grimes at the house near downtown Pensacola. (Insurance Journal)
Was this article valuable?
Here are more articles you may enjoy.